LET’S get one thing straight – oil palm machineries weren’t built for oil palm. Backhoes, tractors, graders – they’re borrowed from other industries, designed for different sectors with less demanding conditions. But oil palm?
It’s relentless, Work throughout the year.
Durability, adaptability and reliability aren’t optional – they’re make-or-break.
Yet breakdowns happen.
Factor in slow repairs and spare part shortages, and a simple failure can mean weeks of lost productivity.
Mechanising oil palm is tough. Unlike uniform greenhouses, estates face harsh weather, seasonal peaks, and rugged terrain – hills, peat and aging trees.
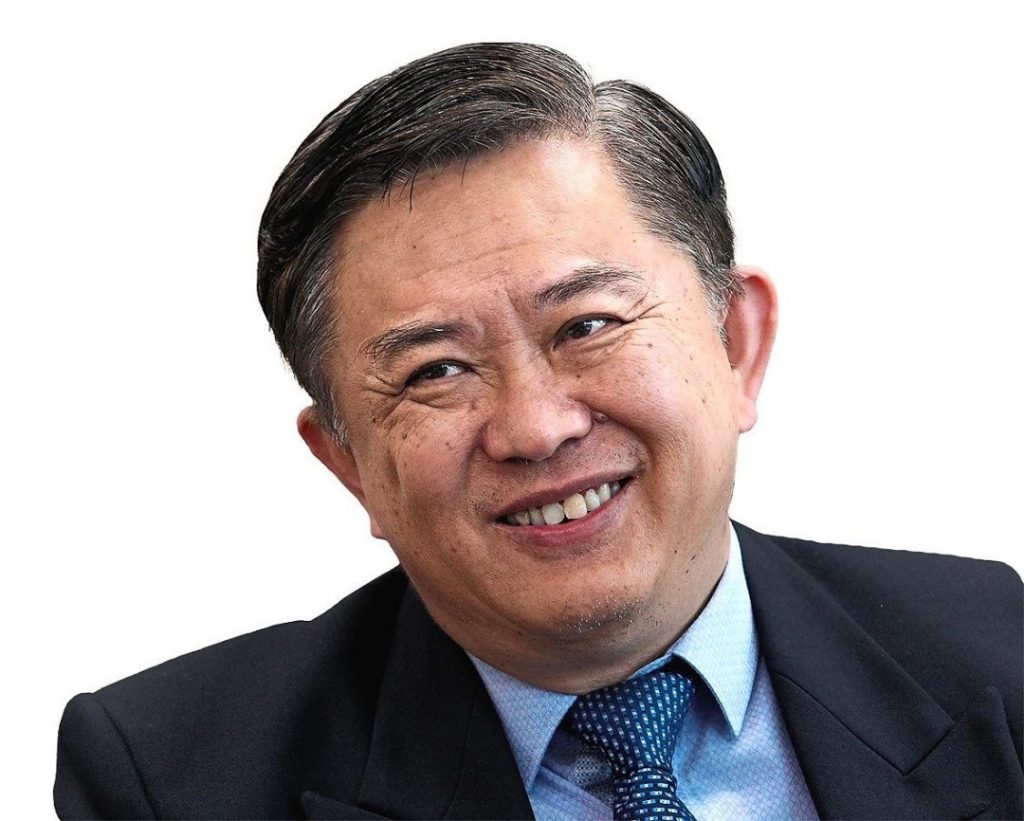
Joseph Tek
And those trees don’t stay put; they grow. The most common DxP Deli and AVROS planting material can shoot up 60 cm a year, hitting 13+ m by age 25. Past 12m, harvesting becomes challenging.
The solution? Replant in time. But we’re not doing it fast enough, especially when prices are good and funds are tight.
By 2027, 2 million hectares – 35pc of Malaysia’s oil palm land – will be filled with overgrown trees. A crisis looms.
Right now, only 17pc of plantations (960,000 ha) have trees in the ideal 4–8-year range where motorised cutters might still work.
Even then, their real-world performance is patchy.
Terrain adds another challenge.
Sabah and Sarawak hold 55pc of Malaysia’s oil palm, with steep hills and sprawling peatlands complicating mechanisation.
Nothing wrong in breeding and using buffaloes in some areas!
The takeaway? No one-size-fits-all fix.
But that’s no excuse to stall. If a tool works on flat land, scale it up.
If it’s viable in other landscape, refine and deploy it. Every win moves the industry forward.
Who’s Driving Oil Palm Mechanisation
Conversation on oil palm mechanisation divides the industry into four camps: The Optimists – convinced the perfect solution is near; The Pessimists – doubt it will ever work at scale; The Pragmatists – see the challenges but push for steady progress; and the Opportunists – chase trends for short-term gains.
Each shapes the debate, but talk alone won’t get the job done.
Without leadership, coordination, and accountability, we’ll be stuck in the same loop a decade from now. Mechanisation isn’t a side project – it’s a long-term mission beyond budget cycles.
Silos lead to fragmented efforts, flashy prototypes, and no real impact. Oil palm is tough to mechanise, but we’ve been growing and harvesting it for over a century. The difference now? We have technologies once thought impossible.
The real question – can they work for oil palm?
Any engagements about oil palm mechanisation, especially harvesting, and you’ll find a crowd – growers, tech-developers, policymakers and corporate leaders – each with their own views, priorities and, let’s be honest, agendas.
Differences in opinion are natural. But too often, the conversation gets tangled in ambitions, selective optimism and a few conveniently ignored realities.
The challenge isn’t just about technology. It’s a stress-test of industry-wide commitment, collaboration and leadership – the kind that delivers real solutions, not just bold claims.
Often, new devices are hyped as the “game-changer” plantations have been waiting for.
Yet, when adoption lags, fingers start pointing at growers – branded as hesitant, old-school or unwilling to invest. But when these so-called breakthroughs hit the field and fizzle out, the blame suddenly shifts.
Now, it’s the growers’ fault for not using them “correctly” or failing to “fully commit.”
Mechanisation needs more than marketing buzz – it needs hard-earned credibility.
A prototype that dazzles in a pilot-scale but stumbles in the field is not a solution.
Growers, who wrestle daily with labour shortages, tough terrains, ageing trees and productivity pressures, have seen one device after another.
Many turn out to be impractical, fragile or simply too costly to be viable. A machine that breaks down mid-harvest or needs constant fixing isn’t mechanisation – it’s just another expensive problem.
Authorities play a crucial role in setting policies, supporting R&D and driving industry-wide progress.
But on the ground, optimism in official reports doesn’t always match the reality of bureaucratic bottlenecks and fragmented efforts.
The real question isn’t whether we’re working on mechanisation – it’s whether we’re working on the right solutions, at the right pace, with the right urgency.
Plantation leaders face their own pressures – to show progress and justify R&D spending. Investments are made, KPIs are monitored.
Yet behind closed doors, many admit that the biggest challenge – efficiently harvesting tall oil palms – remains the unresolved problem.
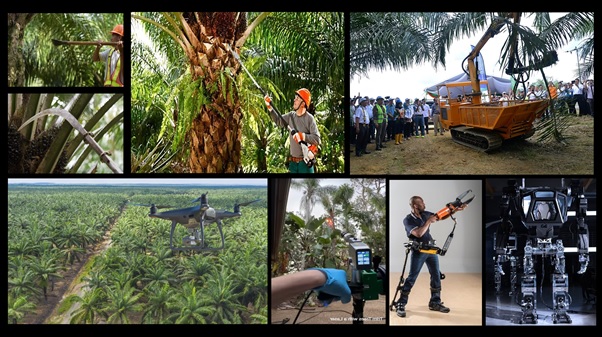
Oil palm harvesting saga: From traditional tools to high-tech innovations – chisels, sickles, motorised, drones, lasers, exoskeletons and robotics.
Mechanisation has to move beyond research papers and boardroom slides. It must work where it truly matters – the field. Technologies like IR4.0 or 5.0 sound impressive, but oil palm plantations aren’t plug-and-play environments.
Unlike annual crops, perennial oil palms grow taller, surrounded by dense canopies, thorny fronds and heavy fruit bunches.
The industry must shift gears – from chasing theoretical breakthroughs to delivering practical, field-tested innovations that appreciates the biological, environmental and operational realities of oil palm plantations.
Harvesting – Half the Workforce
Talk about oil palm harvesting all you want, but without a solid grasp of oil palm biology and ground realities, even the most high-tech solutions risk missing the mark.
Height growth patterns, tricky terrains, harvesting inherent challenges and workforce dynamics aren’t just details – they’re the foundation of whether a mechanisation idea will fly or flop.
Yet, we often hear stakeholders – many who’ve never set foot in an estate – throw around “buzzwords” as if oil palm mechanisation is just another smartphone revolution waiting to happen.
Spoiler alert: oil palms are not iPhones. They don’t shrink to fit in your pocket, and their challenges can’t be solved with an app update.
Mechanisation efforts go way back to the 1980s, improving non-harvesting operations like crop evacuation, fertiliser application, weeding, drones and more. But here’s the catch – these don’t significantly reduce overall labour needs. Why? Because harvesting is where the real manpower is.
Let’s cut to the chase – harvesters make up about 50pc of the workforce in non-mechanised plantations. And with high-yielding planting materials pushing yields to potential 30 tons or more per hectare, that figure could rise to 60-70pc of total workforce.
Yet, many estates already struggle with harvester shortages, leading to crop losses and millions in unrealised revenue – and taxes!
The hard truth? No amount of tech-wizardry will solve oil palm’s labour crunch until harvesting is mechanised in cutting bunches, pruning and stacking fronds and collecting loose fruit.
Labour Shortages: Industry’s Ticking Time Bomb
Yes, tropical oil palm requires less labour per hectare than rubber, cocoa, coffee or sugarcane.
But let’s not kid ourselves – Malaysia’s oil palm industry is in a labour crisis, and it’s not getting better.
Skilled harvesters are in short supply and getting older, and there’s no magic crop swap that will solve the problem – because they need even more workers!
And let’s face it: local workers aren’t coming back.
The days when Malaysians took on 3D (Dirty, Dangerous, Difficult) jobs are long gone.
That ship has sailed, and no amount of wishful thinking will bring it back.
Ironically, the industry’s own success in boosting yields has deepened the crisis.
Better planting materials, advanced agronomy and optimised fertilisation can push productivity higher – but that also means more bunches to harvest.
With more bunches, even more workers are needed, especially during peak seasons or bad weather.
But let’s cut through the noise. Do we actually have cost-effective, scalable and plantation-ready solutions today?
Or are we still stuck in the cycle of flashy prototypes, theoretical models and overpromised tech?
That starts with brutal honesty: what works, what doesn’t, and what it will really take to mechanise oil palm harvesting effectively.
Harvesting: Industry’s Achilles’ Heel
Ever heard of robots climbing coconut trees? Great idea – just not for oil palms.
Unlike coconuts, oil palms come with a fortress of thorns, dense canopies, and frond butts that refuse to cooperate.
Climbing-based mechanisation? Nice try, but not so easy.
Let’s face it – harvesting oil palm is a tough job. As trees shoot past 12 m, even the best harvesters will struggle.
Fewer skilled workers, an aging workforce, and sheer physical exhaustion make manual harvesting a race against time.
The challenge? Any mechanised solution must be cost-effective, boost efficiency, and at least match human productivity.
A tool that costs a fortune but delivers portion the output of a harvester? That’s not innovation – it’s an expensive disappointment.
And let’s not forget loose fruit collection. These tiny powerhouses of oil quality often go ignored, even though they make up a significant part of the yield.
Harvesting Technologies: Hype vs Reality
It’s time for some straight talk. While oil palm mechanisation has made strides, the biggest beast remains untamed – harvesting tall palms.
Many so-called “breakthroughs” skirt around the fundamental issues.
Sure, they make headlines, but can they handle real-world plantation conditions?
Motorised Cutters: Not for tall trees. Can speed up cutting, reduces effort but the vibrations, mobility issues, battery life headaches, and long-term occupational health risks for workers. It is still clunky in reality. Often better suited for pruning than full-scale harvesting.
Drones: Already great for mapping, some degree for pest control, and precision fertilisation. Cons: Battery limits, weather dependency, and payload constraints make harvesting a challenge.
Nice to have, but not a silver bullet. Imagine a fleet of drones grounded by rain while manual harvesters keep going. That’s the reality check.
Exoskeletons: Inspired by Avatar-style suits, designed to reduce physical strain. Cons: Bulky, expensive, limited mobility – plus, try wearing one in a hot, humid plantation! Verdict: Looks cool, but we’re not there yet.
Autonomous Robots: The dream – robots handling harvesting and crop evacuation, no labour worries. Cons: Oil palm trees aren’t uniform; their structure makes robotic harvesting a serious challenge. Verdict: A long-term goal, not a quick fix. Needs major R&D investment before it becomes viable, if can.
Mechanisation isn’t about fancy gadgets – it’s about practical, scalable, and cost-effective solutions.
And until we crack the code for tall palm harvesting, the industry’s “Holy Grail” remains just a dream.
The bottom line?
No single technology will solve the harvesting dilemma overnight.
But a mix of smarter tools, better materials, and targeted innovations may chip away at the problem – one practical step at a time.
Low-Hanging Fruit in Harvesting
While the industry aspires for mechanical marvels that may replace human harvesters, the real opportunity may be staring us in the face – perfecting the tools we already have.
Many of us still can’t expect a machine to outpace a skilled oil palm harvester, slicing through bunches with speed, precision and adaptability?
The best plantation companies – the ones consistently delivering high yields – aren’t sitting around waiting for a breakthrough.
They’ve mastered the art of harvesting and crop evacuation. Even with towering palms, they strive to stick to a disciplined 10-to-15-day harvesting cycle.
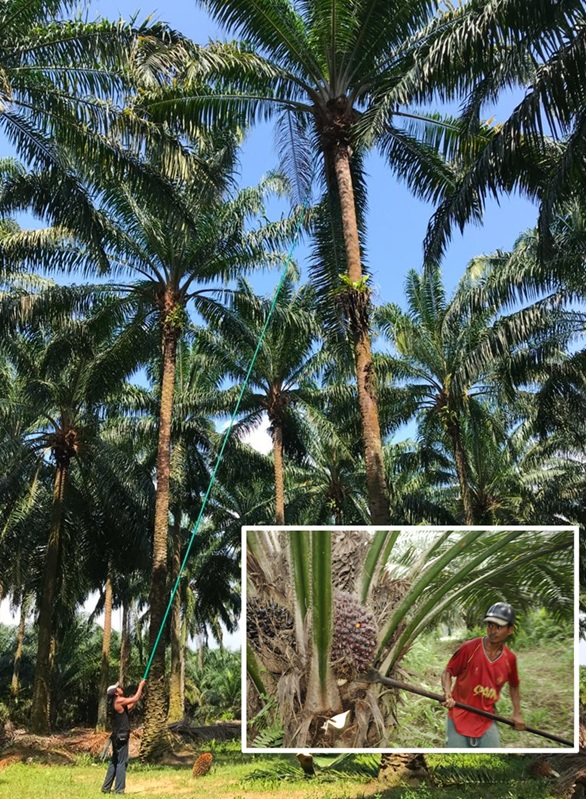
Current harvesting methods for short and even very tall trees using harvesting poles with chisels and sickles.
No excuses. Let that slip, and chaos ensues – a snowballing mess of inefficiency.
Time-motion studies, around for decades, offer a goldmine of insights into harvesting efficiency.
A harvester’s eight-hour shift isn’t just spent cutting bunches – far from it. Less than 30 minutes is actually spent slicing through fruit and fronds.
The other seven-and-a-half hours? Walking with heavy pole, positioning poles amid towering fronds, manoeuvring through uneven terrain and searching for ripe bunches over 360 degree-turn.
If we want to boost productivity, the real battle isn’t in the cutting – it’s in making the rest of the workday less exhausting and more efficient.
Lighter yet durable poles mean better mobility and reduced fatigue. Sharper, tougher sickles mean fewer strokes and faster cuts. Better sharpening tools keep blades razor-sharp for longer.
Oil palms are silica powerhouses.
A single tree holds 4-5kg of silica, while pruned fronds dump 110–131 kg per hectare back into the soil.
If we’re serious about efficiency, stronger, longer-lasting metals should be on the priority list.
These aren’t minor tweaks; they’re silent productivity boosters hiding in plain sight.
Food for Thought
If a harvester only spends 30 minutes daily actually for just cutting, does it make sense to replace them with a machine that might take just longer – positioning itself, adjusting angles and manoeuvring around the palms?
Skilled human harvesters still outperform machines in real-world conditions, instinctively adapting to different heights and frond orientations.
But that doesn’t mean technology has no place. Instead of replacing harvesters, why not empower them?
Drones and rovers can map out ripe bunches before harvesters even step into the field, eliminating wasted time spent searching.
AI-powered detection systems can highlight which palms need attention.
Digitalisation with tracking can optimise harvester routes and more. The real revolution isn’t just in fancy machines – it’s in eliminating inefficiencies that drain time and energy.
Until futuristic solutions arrive – if they ever do – there’s still plenty of room to improve today’s tools.
Poles can be stronger, lighter and extend further without becoming unwieldy.
Material science can offer answers – eg. carbon fibre. The right balance of rigidity, flexibility and weight could make all the difference.
Can sickles be sharper?
Laminated with bonded steel for durability, thin enough for precision but not so fragile that they snap under pressure.
A sickle’s perfect thickness is a delicate balance – too thin and it breaks, too thick and it loses its slicing edge.
Good news: The tools to harvest beyond 12 meters already exist, extending productivity on 25-year-old palms by another three years.
Many South American estates successfully manage even taller palms with high recovery rates.
That’s three more years of revenue, three more years of building funds for replanting – if managed wisely.
This is the immediate way forward.
With the right R&D funding, further improvements could even drive the costs of these tools down for wider adoption.
Harvesters: Backbone Mechanical Workforce
The real power behind the system is human harvesters – the mechanical workforce we already have.
Reward and motivate them with higher pay, bonuses and include proper nutrition.
Support their well-being, and they’ll keep the industry moving while we pursue future solutions.
Treat them well and they will deliver.
The training of new harvesters should also be carefully structured to ensure a smooth transition from novice to skilled workers, aligning their development with the tools available and the varying heights of oil palm trees as they grow.
Additionally, assigning dedicated full-time harvesters allow for optimal utilisation of their skills and time for harvesting task and nothing else.
Oil Palm is Tough. Are We Tougher?
Oil palm is God’s tree-gift of abundance, yet it demands effort, skill and discipline.
Perhaps not every challenge can be solved by effectively by machines – some require perfecting what already works.
Until we crack the harvesting code, human labour remains the backbone.
The Holy Grail of harvesting may still be out there, but real progress with low-hanging fruit is within reach – right now.
The industry is at a crossroads. We need bold decisions, clear strategies and the kind of focus and determination that sent humans to the moon.
Fragmented efforts won’t cut it. What’s needed? Long-term funding and R&D, empowered leadership, serious cross-sector collaboration and results over hype. Whoever solves harvesting will revolutionise the industry.
If we don’t tackle this problem head-on, the industry’s biggest challenge won’t be productivity – it’ll be survival. Mechanise or perish.
Follow our Facebook page ConserveByU for our latest updates.